Design: Forced-air evaporative cooling chamber
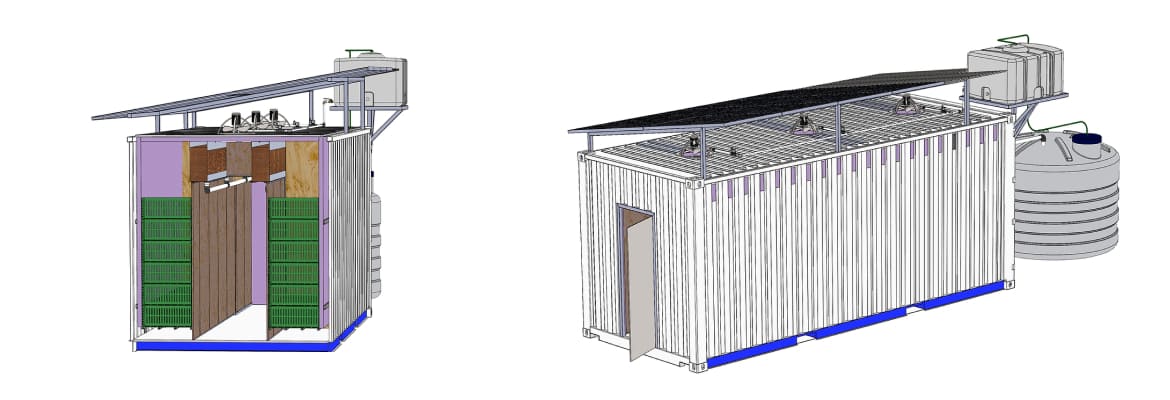
Storing vegetables after harvest without cooling them can lead to spoilage and therefore reduced access to fresh and nutritious food and reduced income for farmers. Most techniques for cooling and storing vegetables rely on vapour-compression refrigeration, which may not be affordable or available for many smallholder farmers, particularly those living in remote, off-grid and low-income areas.
This open-source design for a solar-powered fruit and vegetable cooling chamber offers accessible cold storage for smallholder farmers. The forced-air evaporative design can be built using a shipping container and is specifically designed for preserving produce in hot and dry climates and to help reduce post-harvest losses.
Using one-quarter of the energy of refrigerated cold rooms and at half the cost to build, the cooling chamber is solar-powered, helping smallholder farmers in arid regions and where electricity supply is limited and/or expensive to better preserve and store freshly harvested produce.
The development of the forced-air evaporative cooling chamber was led by Eric Verploegen and researchers from MIT D-Lab as well as MIT's 'Building technology' programme. Research for the development was supported by funding from the Abdul Latif Jameel Water and Food Systems Lab (J-WAFS), in particular, a 2021 J-WAFS Solutions Grant for the research project titled 'Mobile evaporative cooling rooms for vegetable preservation.' Pilot chambers were since constructed in partnership with Solar Freeze in Kibwezi, Kenya and Hunnarshala Foundation in Bhuj, India.
One of the key features of the design, shared publicly via the project website by the MIT D-Lab design team, is the airflow pathway. In this system, industrial exhaust fans draw hot dry air into the chamber and is passed through a porous wet pad, causing water to evaporate and cool the air. The cool and humid air is then forced over the fruits and vegetables placed in crates inside the chamber to improve their shelf life. The air is then directed through the raised floor and to the channel between the insulation and the exterior container wall, and eventually to the exhaust holes near the top of the side walls.
The design documentation provided consists of 6 sections covering the following topics:
1. Introduction
2. Dimensional Design Schematics
3. Airflow System Guidelines
4. Electrical System Guidelines
5. Plumbing System Guidelines
6. Construction Guidelines